On the shore of Lake Como at Moto Guzzi’s factory, there’s a unique, historic building quietly tucked away in a corner of the site that is almost 70 years old. I would like to share my own passion for Moto Guzzi, and my job in Aerodynamic measurements, to explore this iconic building with the reader: Moto Guzzi’s wind tunnel!
Carlo Guzzi had a vision – that with the increasing performance of racing motorcycles, chasing performance improvements would not only be the search for more power, but the intent to use that power more efficiently – by optimising his motorcycles’ aerodynamics.
From his initial concepts in 1950, and working with his older brother, Giuseppe, “Naco”, they constructed, and inaugurated in 1954, the world’s first motorcycle-dedicated wind tunnel. Naco had graduated as a Civil Engineer and designed many of the factory buildings, as well as their own hydro-electric power plant.
Why optimise Aerodynamic performance?
Fighting against the power of the engine pushing the motorcycle forwards is the force of the air slowing the motorcycle down – causing drag. Drag causes turbulence, reduces maximum speed, makes the vehicle unstable, increases wind noise and discomfort and reduces the vehicle’s fuel economy. It’s easy to see that if you can optimise the shape of the motorcycle and rider in the air, significant performance gains can be achieved that are as applicable to a race bike as they are to a road bike…and indeed a bicycle, F1 car or supersonic aircraft.
What is a wind tunnel?
Instead of trying to chase a moving motorcycle with a lot of instrumentation, and trying to measure it’s aerodynamic performance under variable conditions, a wind tunnel is a construction that fixes the vehicle, or a model of it, under steady-state conditions and blows the air across the motorcycle and rider. The air is pulled through the tunnel by a large fan and will simulate real road speeds across the vehicle’s normal speed range.
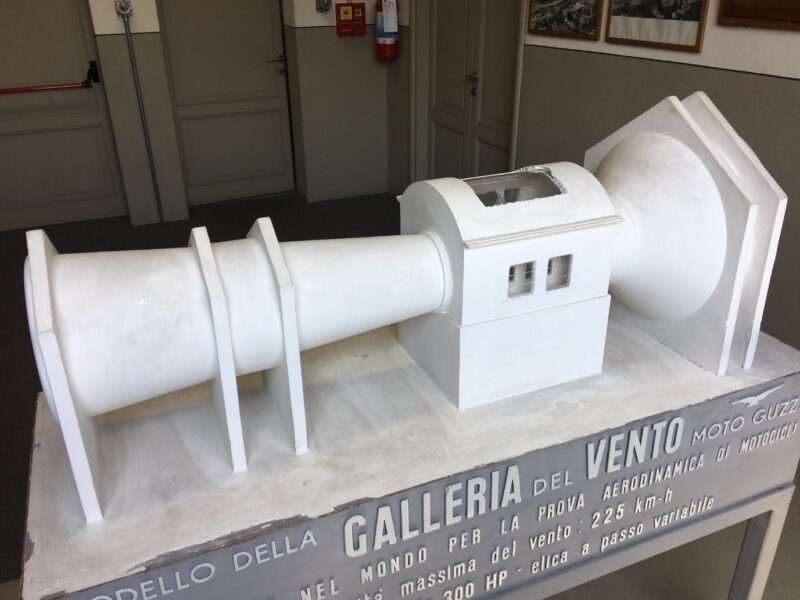
What kind of wind tunnel did Moto Guzzi use?
There are two basic types of wind tunnel – the Gottingen-type and the Eiffel-type, with many variations thereof. They are either used for scale model testing or full-scale, depending on the application. For example, architecture models can be 400:1 scale (0.0025%), Formula 1 cars use 60% scale models and road car and motorcycle manufacturers will use scale models and full-scale (100%) vehicles.
The Gottingen-type wind tunnel is an open or closed-return tunnel. The energised air flows around a tubular circuit of the tunnel loop. With a small input of energy, it gathers momentum efficiently and can reach very high speeds, even trans- or supersonic, if you’re testing an aircraft, and it’s easy to control the ambient conditions and properties of the air. Turning vanes on each corner and anti-turbulence mesh-screens are used to minimise unwanted flow turbulence and resonances. This comes at the price of the air increasing in temperature, meaning a significant cooling system, or heat exchanger, is needed. It also uses a lot more space and is a costly investment to build. These are used in F1 and road car developments where aerodynamic improvements are somewhat easier to achieve and more financially justifiable.
The Eiffel-type wind tunnel is a long straight tube which brings fresh air in at the front, and exhausts it at the exit. The air is affected by external atmospheric changes and the maximum velocity is limited by the maximum power of the motor and fan. They are long and narrow, so take up less floorspace, and are much less costly to construct and operate, but have lower speeds and often unwanted external environmental influences, such as changing atmospheric and temperature conditions, which need to be measured and corrected mathematically.
The Moto Guzzi facility is an Eiffel-type wind tunnel for 1:1 scale – full-scale – motorcycles.
How did the Moto Guzzi Wind tunnel function?
The motorcycle and rider, the “Test Object”, were mounted on a balance frame/pedestal which was free to move longitudinally (with some oil-damping). This was mounted in the 2.6 m (8.5 ft) tall working, or “Test Section”, of the wind tunnel. A honeycomb flow-conditioning screen ahead of the Test Object ensured a smooth, laminar flow of fresh air was pulled-in from outside the through the 8.2 m (26.9 ft) diameter Inlet Contraction. Total length of the wind tunnel was 28.5 m (93.5 ft). A military-surplus, 900 bhp FIAT V12 aircraft engine powered a fan which pulled air over the test object at speeds up to 225 kph (140 mph). This was later upgraded to a 310 hp electric motor and, together with variable motor speed and fan blade pitch (on the three blades), was more economical and efficient, more controllable and created lower noise levels.
As the air hit the front of the motorcycle and rider, the balance was deflected – like a swing-boat in a fairground – proportionally to the aerodynamic profile of the test object. As you might imagine, a solid box on the balance would deflect it much further than one of our beloved motorcycles! This deflection and wind speed were measured and displayed on an illuminated board, like a giant tachometer, the “Scala Convenzionale”, so that the rider could see the relative effects of his riding position, and could change position, accordingly. Aerodynamicists would work to develop and change parts of the bodywork to see how changes affected the drag performance.
The wind speed was measured by pitot tubes mounted in the wall of the wind tunnel data. This is forward facing L-shaped tube with a tiny hole in the end to measure air pressure and correct it for changing Barometric, Static pressure, measured at its static port, where no pressure effect from flow is seen. Check out Mr Daniel Bernoulli’s work for more on this. These pressures were measured on liquid manometers and together with temperature and time were recorded in the adjacent Control Room by the wind tunnel operator, who would also control the wind speed and ensure its safe operation.
The wind tunnel at Mandello Del Lario was first used for testing racing motorcycles and it’s said that Fergus Anderson was the first rider to use it. Racing and road motorcycles, with innovations such as the 500cc V8 racer’s dustbin fairings, were developed and honed there and it continued to be used sporadically into the 1980’s, when the Le Mans Series was tested there and was heavily promoted for its aerodynamic prowess, as seen in the marketing photos and the sales brochures. The 2005 Norge 1200 model was said to be “thoroughly tested” in the Mandello Wind Tunnel, but generally, more modern Moto Guzzi Aero experimentation has utilised specialist external facilities and that is common today, where huge investment in building new wind tunnels is hard to justify, especially for the smaller car and motorcycle manufacturers.
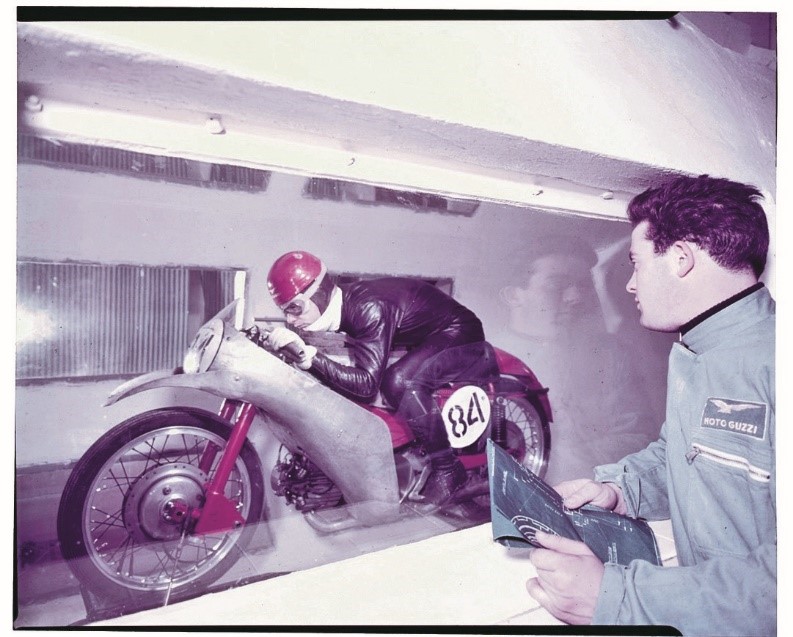
How would this compare to a modern Motorcycle Wind tunnel?
Modern wind tunnels are more complex and sophisticated and demand a significantly higher investment. They are more typically of the Gottingen closed-return type for better control and efficiency. Sophisticated design reduces noise, vibration and turbulence and enhances flow quality and stability.
The motorcycle is mounted on a balance that measures in six axes of movement, X, Y and Z, +ve and -ve, to measure drag, lift (or negative lift, “downforce”), pitch and yaw. The bike may be angled over at up to 60° to simulate aero effects on a turn. It will also be positioned with wheelbase horizontal, as well as under acceleration and braking inclinations, to determine the important Aerodynamic centre of pressure that is essential to stability at varying speeds. The tyres are running on a powered rolling road to simulate the aero effects of moving ground and rotating tyres and brake rotors. Even the tyre tread pattern has an effect on drag! The rolling road, usually a steel or synthetic belt, is likely to be rotatable horizontally to simulate the side loading of the bike from crosswinds, at speed (take note dustbin fairing riders!).
The “rider” will typically be a perfectly 3D-printed representation of a “typical” rider (Pedrosa or Big Dave from the pub?), either in leaning knee-out, prone tucked-in at “V-Max” or sitting-up under braking, positions. A human rider would be unlikely to enjoy sitting in the same position on the bike 24/7 or being able to reproduce the same position he held last week. Chances are that the “rider” is hollow and contains much of the data acquisition equipment.
Parts for the motorcycle will be rapidly designed and 3D- “printed” and attached to the bike, such as wings, profiles, vortex generators or screens, so that many parts can be quickly and inexpensively tried, exchanged and tried again. Often there will be dozens of parts tested, though these are usually pre-screened by Computational Fluid Dynamics, CFD, computer simulations to limit the number of physical tests required. Focus of the tests is key to operational efficiency as many runs are costly in time and money.
Hundreds of tiny pressure sensors, or more likely pressure scanners, are fitted to the motorcycle and the “rider” to measure aerodynamic pressures on every surface. Pressure tappings are accurate holes in the surface and these are tubed to the scanners. Scanners would also be tubed to Kiel rake arrays or pitot probes, attached to the bike, to map external air pressure profiles and hence the aerodynamic signature mapped around the whole motorcycle and its immediate surroundings.
All of this pressure and temperature data is recorded via an Ethernet connection on every channel at up to 1000 readings per second, detailing how vortices, transients and eddies change during a run, with the data being analysed and used to construct new parts that are ever more sophisticated and provide more aerodynamic performance.
Additionally, advanced techniques such as Laser Doppler Anemometry (LDV) or Particle Image Velocimetry (PIV) are used to capture velocity profile “slices”, through the air, across the entire wind tunnel. Boundary layers, where air is considered to be stagnating on surfaces, are also assessed.
What about the iconic wool tufts, smoke wands and “flo-viz” (flow visualisation or pressure-sensitive) paint? They still have a place to play in outline visual estimates…and for great marketing images, but mostly data needs to be very high integrity, fast and accurate, as well as being able to be gathered as millions of data points and stored for post-processing and analysis.
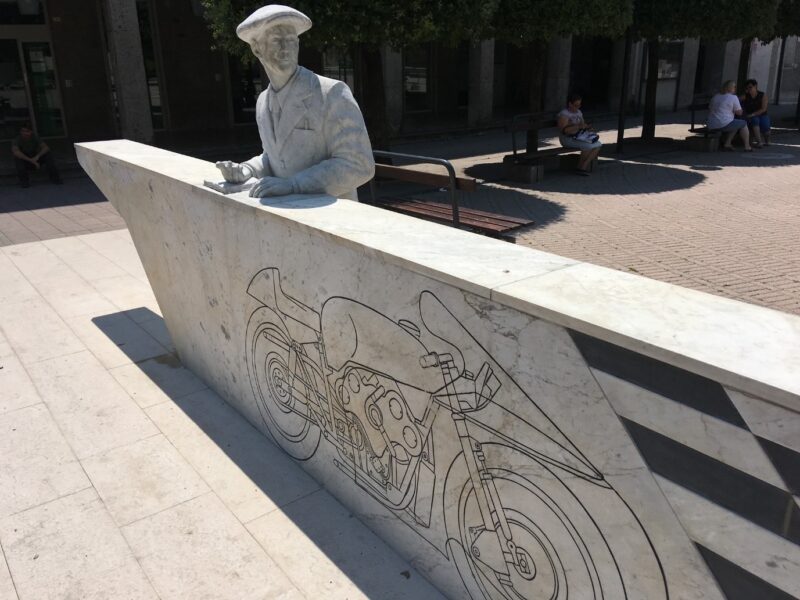
How does the future look for Motorcycle Aerodynamics?
Motorcycle manufacturers will accelerate their aerodynamic developments. Reductions in drag, noise, fuel consumption, emissions and regulations will drive this. Turbulence causes rider fatigue, higher wind noise and discomfort (try riding with your visor up or a scarf tugging at your neck!).
Ironically, at the expense of increasing drag, more downforce will improve braking and straight-line stability, cornering capability and anti-wheelie – which, with wheelspin, is often the limiting factor in race motorcycle acceleration. However, whilst downforce improves traction when upright, it will negatively affect cornering ability at extreme lean angles. As you may see, Aerodynamics is optimised in different ways for different applications, and there is always a compromise involved.
The “Active Aerodynamics” that are seen in cars, or often hidden, such as moveable aero sections, like wings and ducts, or changing ride heights, are becoming more common. Whilst radiators and coolers need maximum airflow at low speed, for example, they create drag at high speed, so isolating them, fully or partially, can be highly beneficial. Cool air helps engine and braking efficiency, but with a drag penalty. Changes in profile can use motorised or hydraulically actuated flaps, “lamella”, or “aero-elastic” materials can conveniently flex under air pressure. Thus, aerodynamics plays a large part in meeting strict environmental, economy and emissions targets.
Helmets and clothing, as in the cycling world, will increasingly use Aerodynamic profiling to improve their performance and comfort. Aerodynamics in MotoGP become more sophisticated, often importing Formula 1 personnel and their innovations, especially with a drive for downforce to help get their huge power to the back tyre. As with Formula 1, rules are brought-in to limit the exponential growth of this technology advancement to keep costs in-check and the sport competitive and entertaining.
Marketing continues the drive to make road vehicles look more like their racing counterparts, so just as you see more vents, wings, diffusers and aero sections on “less exotic” road cars, you’ll see more MotoGP derived aero designs reach road bikes to help the buyer aspire to look more like their racing hero.
As Electric motorcycles develop further, aerodynamic optimisation plays an important part in both cooling batteries/motors to ensure optimal discharge temperature, but also in extending battery range by drag reduction – a 10% reduction said to enhance operable range by over 5% – at highway speeds.
As for the Wind Tunnel? Increasingly sophisticated CFD use, plus more on-board measurements, such as EvoScann® pressure scanners, on test bikes may reduce the use of wind tunnels, but they will continue to play a major role in motorcycle aerodynamics for the foreseeable future. What was started by the wonderful, iconic Moto Guzzi wind tunnel and it’s highly respected, innovative engineers, will continue to impact future generations.
If you have chance to visit the wonderful Mandello Del Lario factory and museum, I hope you pause in the corner of the site and spare a thought for Moto Guzzi’s experimental engineers and I hope my article may help you understand a little more about their famous wind tunnel and why they built it.
About the Author: Iain Gordon has been passionate about Moto Guzzi since he was 15. He currently has Le Mans II and Daytona RS, as well as MV Agusta, motorcycles. His role in Export Sales of Wind Tunnel and On-vehicle Aerodynamic measurement instrumentation, such as Scanivalve & EvoScann pressure scanners and Vectoflow multi-hole flow/pressure probes, takes him to the major motorsport and road car and motorcycle facilities of the world – (secrecy and confidentiality agreements prevent him telling you anything much about them) – except when he’s at home writing his first article on motorcycle aerodynamics.